Nonwoven fabric, sometimes spelled non-woven fabric, is an engineered material that feels and looks somewhat like cloth. However, its structure isn’t created through traditional methods like spinning and weaving. Instead, it’s made by bonding or tangling staple fibers (which are short) and long fibers (which are continuous) together using chemical, mechanical, thermal, or solvent treatments. Unlike conventional textiles that are either woven with interlacing yarns or knitted with interlocking loops, nonwoven fabric is produced directly from individual fibers. This direct fiber-to-fabric approach is a key characteristic that distinguishes nonwoven fabric from traditional textiles.
The raw materials for nonwoven fabric can include short fibers, such as cotton or wool, which have a limited length, and long fibers, like continuous filaments formed through melt extrusion. These fibers are joined together in various ways, including chemical bonding with adhesives, mechanical entanglement through processes like needle punching or hydroentangling (spunlace), thermal bonding using heated rollers or hot air, and even solvent treatments.
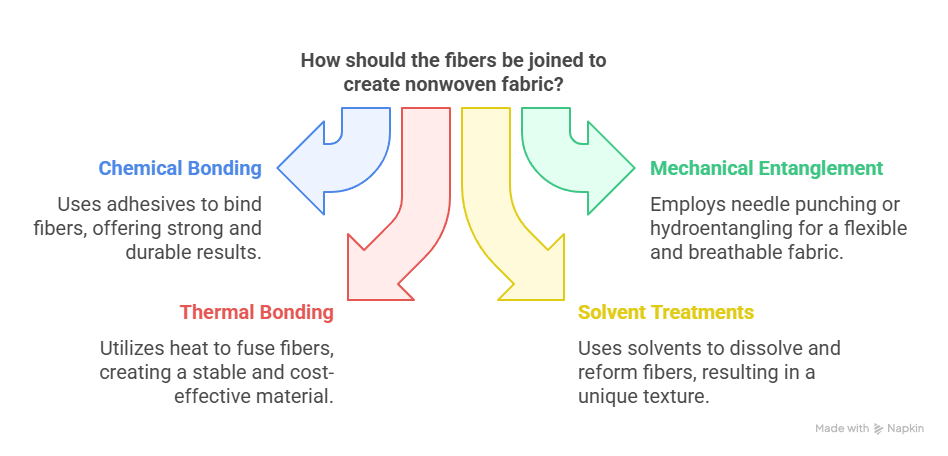
Due to its unique manufacturing process and customizable properties, nonwoven fabric finds applications in a wide range of fields. These include medical and hygiene products, apparel, the automotive industry, filtration materials, construction, geotextiles, and personal protective equipment. The performance of nonwoven fabric can be designed and adjusted to meet specific application needs, such as absorbency, liquid repellency, elasticity, strength, flame retardancy, washability, cushioning, filtration, and acting as a bacterial barrier. This allows for a good balance between the product’s lifespan and its cost.
This report aims to provide a comprehensive overview of nonwoven fabric, covering its definition, historical development, main manufacturing processes, the principles and characteristics of different types of nonwoven fabric, commonly used raw materials and their properties and applications, the various performance characteristics of nonwoven fabric and the factors that influence them, specific application examples across different industries, a comparison with traditional textiles, current market trends, major manufacturers and consumer regions, and a look at the future of nonwoven fabric technology and applications. Through an in-depth examination of these aspects, this report intends to serve as an authoritative reference for industry professionals and academic researchers seeking a thorough understanding of nonwoven fabric.
A Look at the History of Nonwoven Fabric
The origin of nonwoven fabric isn’t a modern invention; its history dates back to ancient times. Early civilizations utilized natural fibers like reeds, grasses, and rushes, creating everyday items such as mats or floor coverings through weaving or felting techniques. These early attempts, though rudimentary, embodied the basic principle of modern nonwoven fabric – directly assembling fibers into a sheet-like structure.

The true beginnings of the modern nonwoven fabric industry can be traced to the 19th century. At that time, the textile industry in England was well-developed, producing a significant amount of textile waste. A textile engineer named Garnett invented a special carding machine capable of recycling this waste and reprocessing it into fibers, initially used mainly for pillow stuffing. Garnett’s invention is considered a major milestone in the history of modern nonwoven fabric development. Subsequently, some manufacturers began experimenting with mechanical methods (like needle punching) or chemical methods (like using glue) to bond these recycled fibers together, forming the early versions of modern nonwoven fabric.
The emergence of synthetic fibers in the 1930s and 1940s provided a significant boost to the development of nonwoven fabric. The creation of synthetic polymers like nylon and polyester allowed for the design and production of nonwovens with specific performance characteristics tailored to different needs. In 1942, in the United States, a material made by bonding fiber webs first began industrial production and was officially named “Nonwoven fabric“. This event marks the formal birth of the modern nonwoven fabric industry.
Over the following decades, the production technology for nonwoven fabric continued to advance. In the 1950s and 1960s, new production methods like meltblowing and spunbonding were invented. Compared to traditional drylaid web formation techniques, these new processes could produce lighter and more durable nonwovens, expanding their range of applications. In 1962, the American Society for Testing and Materials (ASTM) first provided a clear written definition of nonwoven fabric, signifying the industry’s widespread recognition of nonwoven fabric as an independent textile material.
Entering the 1970s and 1980s, the demand for nonwoven fabric in the hygiene products industry began to grow rapidly. The widespread use of disposable diapers, sanitary napkins, and wet wipes significantly drove the production and application of nonwoven fabric. From the 1990s to the present, with continuous technological innovation and development, the nonwoven fabric industry has continued to expand, and its applications have broadened from traditional hygiene and medical products to numerous other fields, including automotive, construction, agriculture, and filtration.
The early emergence of nonwoven fabric was closely linked to the emphasis on resource reuse, which to some extent reflects its inherent sustainability, although the driving factors at the time differed from today’s environmental awareness. The development of synthetic polymers was a crucial turning point, making it possible to produce customized nonwoven fabrics with performance characteristics beyond the capabilities of natural fibers. The formal definition of nonwoven fabric by ASTM in 1962 marked the official recognition of this material as a textile category distinct from woven and knitted fabrics, laying the foundation for industry standardization, research, and further development.
Main Manufacturing Processes for Nonwoven Fabric
The manufacturing processes for nonwoven fabric are diverse. Based on how the fiber web is formed, they can be broadly categorized into three main types: drylaid web formation, wetlaid web formation, and meltblown web formation.

Drylaid web formation is one of the earliest and most widely used methods. It primarily includes the following two processes:
- Carding: This process borrows from traditional textile carding techniques used in yarn production. Through a carding machine, pre-opened and mixed fibers are separated and aligned to form a fluffy fiber web. Carding is suitable for short fibers (typically between 20 and 60 millimeters in length) or long fibers (between 50 and 150 millimeters in length). Fiber webs produced using this method usually have higher strength in the machine direction (the direction the machine runs) and relatively lower strength in the cross direction. To improve the cross-directional strength of the fiber web, carding machines can be equipped with randomizing rollers to make the fiber arrangement more random. Carding technology, as an early stage in nonwoven fabric manufacturing, utilizes existing textile machinery. However, its limitations in fiber alignment directionality make subsequent bonding or layering techniques crucial for achieving the desired fabric performance.
- Airlaid: Airlaid technology uses air currents to disperse fibers, which are then deposited onto a moving screen to form a uniform fiber web. This process is particularly suitable for processing very short fibers, such as wood pulp fibers, or mixtures of short-cut synthetic fibers. Additionally, the airlaid process can mix superabsorbent powders or fibers into the fiber web during its formation, creating nonwovens with high absorption properties. Fiber webs formed through airlaid typically have high bulk and relatively uniform strength in all directions. The ability of airlaid technology to process extremely short fibers, including wood pulp, gives it a unique advantage in producing absorbent products. Directly incorporating superabsorbent materials into the fiber web formation process further enhances its value in the hygiene products sector.
Wetlaid web formation is a method similar to traditional papermaking. It first disperses short fibers in water or another liquid medium to form a fiber suspension. This suspension is then fed to a web-forming device, where the fibers are deposited onto a moving screen through filtration, forming a fiber web. Finally, the web is dewatered and dried to obtain the nonwoven fabric. Wetlaid is suitable for various types of short fibers, including natural fibers, synthetic fibers, and even glass fibers, ceramic fibers, and carbon fibers. This process can form highly uniform, high-density fiber webs and offers high precision in weight and thickness control. Wetlaid technology is widely used in the production of industrial materials, food packaging materials, and medical and hygiene products. The similarity between wetlaid and papermaking processes provides it with mature technology and good scalability. Its ability to handle a variety of fibers, including inorganic fibers, expands its applications in high-performance fields where traditional textile fibers are not suitable.
Meltblown web formation directly uses polymer melts to form fiber webs. It mainly includes the following two processes:
- Meltblown: In the meltblown process, molten polymer is extruded through fine nozzles in a spinneret. Simultaneously, it’s subjected to high-speed hot air streams that stretch and cool the polymer, forming extremely fine fibers. These fibers typically have a diameter between 1 and 5 micrometers, resulting in a very high surface area and porosity. Nonwoven fabric produced by the meltblown method is primarily used for filtration materials (such as the filter layer in medical masks), oil-absorbing materials, and hygiene products. Because meltblown fibers have low strength, they are often combined with other nonwovens (like spunbond nonwovens) to improve overall strength. The unique ability of meltblown technology to produce ultrafine fibers makes it indispensable in high-efficiency filtration, especially playing a crucial role in medical masks. However, its strength is typically low, so it often needs to be combined with other nonwovens.
- Spunbond: The spunbond process first extrudes molten polymer through spinnerets to form continuous filaments. These filaments are then stretched and thinned through cooling, air drawing, or mechanical drawing. The thinned filaments are laid down onto a moving conveyor belt to form a fiber web. Compared to meltblown fibers, spunbond filaments are usually thicker, so the resulting nonwoven fabric has higher strength and durability. Spunbond nonwovens are mainly used in hygiene products (such as the top and bottom layers of diapers), geotextiles, filtration materials, and the automotive industry. The spunbond process is a continuous production process with high efficiency. The continuous filament production and high-strength characteristics of spunbond technology make it suitable for applications requiring durability and structural integrity. The continuous production process also makes it cost-effective and widely applicable.
In addition to the main manufacturing processes mentioned above, there are several other methods for producing nonwoven fabrics, such as:several other methods for producing nonwoven fabrics

- Spunlace (Hydroentanglement): Uses high-pressure water jets to entangle fibers in a web, creating a nonwoven fabric with softness, good drape, and high absorbency.
- Needlepunch (Needlefelting): Uses barbed needles to repeatedly puncture a fiber web, mechanically entangling the fibers to form a thick and durable nonwoven fabric.
- Thermal Bonding: Uses heat and pressure to melt and bond thermoplastic fibers within a web.
- Chemical Bonding: Uses adhesives (like latex) to bond fibers within a web together.
- Stitch Bonding: Uses sewing threads to stitch a fiber web together, increasing its strength and stability.
- Flashspun: Uses high-speed jets of polymer solution, causing it to instantly evaporate and form a high-strength, high-barrier nonwoven fabric.
Different bonding methods allow for fine-tuning the performance of nonwoven fabric. Mechanical bonding provides softness and good drape, while thermal and chemical bonding can enhance strength and other specific properties.
Manufacturing Principles and Characteristics of Different Types of Nonwoven Fabric
Different types of nonwoven fabric exhibit significant differences in manufacturing principles and final product characteristics due to variations in their manufacturing processes.

Spunbond nonwoven fabric is manufactured by extruding molten polymer (such as polypropylene or polyester) from spinnerets to form continuous filaments. These filaments are directly laid down into a web-like structure after being stretched by air or mechanical force. Subsequently, the fiber web is reinforced by thermal rolling, ultrasonic bonding, or chemical bonding. Spunbond nonwoven fabric is characterized by high strength, good durability, and relatively low cost due to its simple production process. Additionally, spunbond nonwoven fabric has good breathability, but its filtration performance is typically moderate.
The manufacturing principle of meltblown nonwoven fabric is similar to spunbond, but its key feature is that the polymer melt, after being extruded from the spinneret, is immediately subjected to high-speed, high-temperature air streams that stretch it into very fine fibers. These ultrafine fibers are then collected on a receiving device to form a fiber web. Meltblown nonwoven fabric is characterized by very fine fiber diameters (typically 1-5 micrometers) and small pore sizes, resulting in extremely high filtration efficiency. At the same time, meltblown nonwoven fabric is also relatively soft, but its overall strength is lower due to the fine and short nature of the fibers.
Needlepunch nonwoven fabric is manufactured by first arranging fibers into a web using a carding machine or airlaid machine, and then repeatedly puncturing the fiber web with barbed needles on a needle punching machine. When the needles pass through the fiber web, the barbs catch the fibers and cause them to entangle within the web, forming a nonwoven fabric with a certain strength. Needlepunch nonwoven fabric is characterized by being thick, bulky, having high strength and good elasticity, and relatively low production cost, making it widely used in various fields.
The manufacturing principle of spunlace nonwoven fabric involves first forming a fiber web through methods like carding or wetlaid web formation, and then using high-pressure water jets to spray the fiber web. The impact force of the high-speed water flow causes the fibers in the web to undergo intense movement and entanglement, forming a nonwoven fabric with a certain strength. Spunlace nonwoven fabric is characterized by a soft hand feel, good drape, strong absorbency, and relatively high strength. Its appearance and feel are quite similar to traditional textiles.
Airlaid nonwoven fabric is manufactured by using air currents to transport short fibers (such as wood pulp fibers, synthetic short fibers, or their mixtures) into a web-forming machine. The air currents cause the fibers to disperse evenly and deposit onto a screen to form a fiber web. The formed fiber web is then reinforced by thermal bonding (using heat-fusible fibers), latex bonding, or hydrogen bonding. Airlaid nonwoven fabric is characterized by being bulky, soft, having excellent absorbency, and relatively uniform strength in all directions due to the random arrangement of fibers.
The manufacturing principle of wetlaid nonwoven fabric involves dispersing short fibers (which can be natural, synthetic, or inorganic) in water to form a fiber suspension with a certain concentration. This suspension is then fed into a web-forming machine, where the fibers are filtered onto a screen to form a fiber web using a process similar to papermaking. The fiber web is then dewatered and dried to obtain the nonwoven fabric. Depending on the final product requirements, wetlaid nonwoven fabric can also undergo post-treatments such as thermal bonding or chemical bonding. It is characterized by good fiber web uniformity, high density, controllable strength through the selection of different fibers and bonding methods, and the ability to use various types of fibers.
Nonwoven Fabric Manufacturing Process Flow, Main Equipment, and Key Parameters
Different nonwoven fabric manufacturing processes have their own unique flows, required main equipment, and key parameters that influence the final product performance.
Taking spunbond as an example, its specific process flow typically includes the following steps: First, polymer chips are melted in an extruder; then, the molten polymer is precisely metered by a melt pump and extruded through a spinneret to form long, thin melt filaments; these filaments are cooled and solidified by cooling air or water and then stretched by a drawing system to reduce their diameter and achieve a certain orientation; subsequently, the stretched filaments are laid down onto a moving conveyor belt to form a uniform fiber web; finally, the fiber web is fixed and shaped by a hot rolling machine under high temperature and pressure, or by chemical adhesives, and ultimately wound into rolls. The main equipment used in this process includes an extruder, melt pump, spinneret, cooling system, drawing system, web laying machine, hot rolling machine or adhesive spraying equipment, and a winding machine. Key parameters affecting the performance of spunbond nonwoven fabric include the type and molecular weight of the polymer, melt temperature, extrusion rate, draw ratio, web laying speed, and the temperature and pressure during the bonding process.

The process flow for meltblown is as follows: Polymer chips are melted in an extruder, then metered by a melt pump and extruded through a spinneret; simultaneously, high-speed, high-temperature hot air streams are blown from both sides of the spinneret, stretching the melt filaments into ultrafine fibers; these ultrafine fibers are collected on a receiving device under the action of the air stream, forming a bulky fiber web; the fiber web can be reinforced by its own entanglement or by subsequent slight thermal bonding, and finally wound into rolls. The main equipment in this process includes an extruder, melt pump, spinneret, hot air heater, air compressor, fiber collecting device, and a winding machine. Key parameters affecting the performance of meltblown nonwoven fabric include the type and melt flow index of the polymer, melt temperature, extrusion rate, the temperature and flow rate of the hot air, and the distance from the spinneret to the receiving device.

The process flow for needlepunch typically involves: first, preparing the fibers, including opening, mixing, and carding; then, forming a fiber web of a certain thickness and density using a web laying machine; next, the fiber web is fed into a needle punching machine, where needles on the machine repeatedly puncture the web, causing the fibers to entangle with each other; finally, post-processing such as hot rolling or coating can be performed according to product requirements. The main equipment in this process includes an opening machine, mixing machine, carding machine or airlaid machine, needle punching machine, and various post-processing equipment (such as a hot rolling machine or coating equipment). Key parameters affecting the performance of needlepunch nonwoven fabric include the type and specifications of the fibers, the weight of the fiber web, the needle punching density (number of punches per square centimeter), the needle penetration depth, and the type of needles used.

The process flow for spunlace involves: first, preparing the fibers, which can be done by drylaid web formation methods such as opening, mixing, and carding, or by wetlaid web formation; then, pre-wetting the fiber web to reduce fiber breakage during the spunlace process; next, the fiber web is fed into a spunlace machine, where high-pressure water jets sprayed from spinnerets impact the web, causing the fibers to entangle with each other; the entangled fiber web is then dewatered by a vacuum dewatering machine to remove excess water, followed by drying in a drying machine, and finally wound into rolls. The main equipment in this process includes an opening machine, mixing machine, carding machine or wetlaid machine, spunlace machine, vacuum dewatering machine, drying machine, and a winding machine. Key parameters affecting the performance of spunlace nonwoven fabric include the type and length of the fibers, the weight of the fiber web, the pressure of the water jets, the type and arrangement of the nozzles, and the running speed of the conveyor belt.

The process flow for airlaid involves: first, using a defibration machine (such as a hammer mill) to break down the fiber raw material (such as wood pulp) into individual fibers; then, using air currents to transport these fibers into an airlaid machine, where they are uniformly laid down on a screen under the action of the air currents to form a fiber web; the formed fiber web usually needs to be bonded and reinforced by spraying with an adhesive (such as latex), heating with hot air to melt heat-fusible fibers, or using the hydrogen bonds of the fibers themselves; finally, the bonded fiber web is wound into rolls. The main equipment in this process includes a defibration machine, airlaid machine, bonding equipment (such as a hot air oven or spraying equipment), and a winding machine. Key parameters affecting the performance of airlaid nonwoven fabric include the type and length of the fibers, the weight of the fiber web, the speed of the air currents, the type and amount of adhesive used, and the temperature during the bonding process.

The process flow for wetlaid involves: first, processing the fiber raw material through a pulping machine to disperse it in water and form a fiber slurry with a certain concentration; then, transporting the slurry through pipes to a flow box and uniformly spraying it onto a moving forming screen; below the screen, there is usually a vacuum suction box used to remove water from the slurry, causing the fibers to form a wet fiber web on the screen; the wet fiber web is further dewatered by press rolls and then transported to a drying machine for drying; depending on the final product requirements, the dried fiber web can undergo treatments such as thermal bonding or chemical bonding, and finally wound into rolls. The main equipment in this process includes a pulping machine, mixing tank, flow box, forming screen, vacuum suction box, press rolls, drying machine, and a winding machine. Key parameters affecting the performance of wetlaid nonwoven fabric include the type and length of the fibers, the concentration of the slurry, the speed of the slurry flow, the running speed of the screen, the dewatering pressure, and the drying temperature.

Common Raw Materials for Nonwoven Fabric
The types of raw materials used for nonwoven fabric are numerous and can be categorized based on their origin as natural fibers, synthetic fibers, and regenerated fibers. Different raw materials impart different properties and applications to the nonwoven fabric.

Polypropylene (PP) is one of the most commonly used synthetic fibers in the production of nonwoven fabric. Its properties include high strength, good chemical corrosion resistance, strong hydrophobicity, low cost, and ease of melt processing through heating. The advantages of polypropylene nonwoven fabric lie in its lightweight nature, durability, moisture resistance, good electrical insulation, ease of processing, and recyclability. However, its disadvantages include poor UV resistance, limited high-temperature resistance, difficulty in dyeing, and relatively poor bonding ability. Due to these properties, polypropylene nonwoven fabric is widely used in hygiene products (such as baby diapers and sanitary napkins), medical supplies (such as masks and surgical gowns), geotextiles, packaging materials, and automotive interiors.
Polyester (PET) is another important synthetic fiber commonly used in the production of nonwoven fabric. The properties of polyester include high strength, good elasticity, good heat resistance, good acid resistance, and low moisture absorption. The advantages of polyester nonwoven fabric are its durability, wrinkle resistance, ease of dyeing, good dimensional stability, and relatively moderate cost. Its disadvantages include poor alkali resistance, tendency to pill, and lower moisture absorption compared to natural fibers. Polyester nonwoven fabric is widely used in geotextiles, filtration materials, automotive interiors, building materials, packaging materials, and medical supplies.
Rayon/Viscose is a regenerated cellulose fiber also frequently used in nonwoven fabric production. Its properties include good moisture absorption, softness, good drape, and ease of dyeing. The advantages of rayon nonwoven fabric are its comfortable wear, good breathability, and relatively low cost. However, its disadvantages include low wet strength, tendency to shrink, poor abrasion resistance, and potential environmental concerns related to its production process. Rayon nonwoven fabric is mainly used in hygiene products (such as wet wipes and facial masks), medical supplies, garment linings, and household goods.
Cotton is a natural fiber also commonly used in the production of nonwoven fabric. Its properties include good moisture absorption, softness, good breathability, and good skin-friendliness. The advantages of cotton nonwoven fabric are its natural renewability, good biodegradability, and comfortable wear. However, its disadvantages include relatively high cost, lower strength compared to synthetic fibers, and tendency to wrinkle. Cotton nonwoven fabric is widely used in hygiene products (such as diapers and sanitary napkins), medical supplies, household goods, and agricultural coverings.
Besides the main raw materials mentioned above, some other commonly used raw materials include:

- Nylon/Polyamide: Characterized by high strength, abrasion resistance, and good elasticity, often used in automotive interiors and filtration materials.
- Polyethylene: Exhibits good waterproof and chemical corrosion resistance, commonly used in packaging materials and geotextiles.
- Bio-based plastics: Biodegradable and environmentally friendly, often used in packaging and hygiene products.
- Recycled fibers: Offer the advantages of being environmentally friendly and reducing costs, can be used in the production of various nonwovens.
- Fiberglass: High-temperature resistant and strong, commonly used in filtration materials and building materials.
- Carbon fiber: Lightweight, high-strength, and electrically conductive, often used in aerospace and automotive industries.
To provide a clearer overview of the properties and applications of common nonwoven fabric raw materials, the following table summarizes the key information:
Raw Material | Main Properties | Main Advantages | Main Disadvantages | Main Applications |
Polypropylene (PP) | High strength, chemical resistance, hydrophobic, low cost, heat-fusible | Lightweight, durable, moisture-resistant, good insulation, easy to process, recyclable | Poor UV resistance, limited heat resistance, difficult to dye, poor bonding | Hygiene products, medical supplies, geotextiles, packaging, automotive interiors |
Polyester (PET) | High strength, good elasticity, good heat resistance, good acid resistance, low moisture absorption | Durable, wrinkle-resistant, easy to dye, good dimensional stability, moderate cost | Poor alkali resistance, tendency to pill, lower moisture absorption than natural fibers | Geotextiles, filtration, automotive interiors, construction, packaging, medical supplies |
Rayon (Viscose) | Good moisture absorption, soft, good drape, easy to dye | Comfortable, breathable, relatively low cost | Low wet strength, tendency to shrink, poor abrasion resistance, potential environmental issues | Hygiene products, medical supplies, garment linings, household goods |
Cotton | Good moisture absorption, soft, breathable, skin-friendly | Natural renewable, good biodegradability, comfortable | Relatively high cost, lower strength than synthetic fibers, tendency to wrinkle | Hygiene products, medical supplies, household goods, agricultural coverings |
Nylon | High strength, abrasion resistance, good elasticity | Durable, elastic | Higher moisture absorption | Automotive interiors, filtration materials |
Polyethylene | Good waterproof, chemical resistance | Waterproof, chemical resistant, low cost | Lower strength, poor heat resistance | Packaging materials, geotextiles |
Bio-based plastics | Biodegradable | Environmentally friendly | Performance may not match traditional plastics | Packaging, hygiene products |
Recycled fibers | Environmentally friendly | Lower cost | Performance may be lower | Various nonwovens |
Fiberglass | High heat resistance, high strength | High heat resistance, high strength, chemical resistance | Brittle, difficult to process | Filtration materials, building materials |
Carbon fiber | Lightweight, high strength, conductive | Lightweight, high strength, conductive | High cost | Aerospace, automotive industry |
Performance and Characteristics of Nonwoven Fabric and Their Influencing Factors
The wide range of applications for nonwoven fabric is largely due to its diverse performance characteristics. These properties can be customized by selecting different raw materials and adjusting the manufacturing processes.

Strength is a crucial indicator of the performance of nonwoven fabric. The strength of nonwoven fabric is influenced by various factors, including the type of fibers used, the structure of the fiber web, the bonding method, and the degree of bonding. For example, spunbond and needlepunch nonwovens typically exhibit high strength. Additionally, process parameters such as the weight of the fiber web, the direction of fiber alignment, and the density of needle punching significantly impact the strength of nonwoven fabric. By carefully selecting raw materials and controlling the manufacturing process, the strength can be tailored to meet different application requirements, allowing nonwoven fabric to replace traditional textiles in many high-strength applications.
Absorbency is a key performance characteristic for nonwoven fabric in applications such as hygiene and medical products. The absorbency of nonwoven fabric primarily depends on the fiber materials used (such as hydrophilic fibers like cotton and rayon) and the pore structure of the fiber web. Airlaid and spunlace nonwovens typically have high absorbency due to their bulky structure and fiber characteristics. For some hydrophobic synthetic fibers, absorbency can be improved by using hydrophilic finishing agents. Through material selection and process optimization, the absorbency of nonwoven fabric can be precisely controlled, which is crucial for products like diapers, wet wipes, and medical dressings.
Filtration is an important application characteristic of nonwoven fabric in air and liquid purification. The filtration performance of nonwoven fabric is closely related to factors such as fiber diameter, fiber web pore size, porosity, and whether it has undergone electrostatic treatment. Meltblown nonwovens typically have excellent filtration performance due to their fine fibers and high porosity. Additionally, electrostatic charging treatment can significantly improve the filtration efficiency of nonwoven fabric for fine particles. By controlling pore size and even imparting electrostatic charge, nonwoven fabric can achieve the required filtration levels for various applications, from air purification to medical barriers.
Softness is an important indicator of the comfort of nonwoven fabric, especially in applications involving direct skin contact. The softness of nonwoven fabric is influenced by various factors, including fiber fineness, fiber web structure, bonding method, and post-processing techniques. For example, spunlace and airlaid nonwovens typically have high softness. Additionally, post-processing techniques such as mechanical stretching and chemical softener treatments can further improve the softness of nonwoven fabric. By selecting appropriate fibers, optimizing fiber web formation, and using specific post-processing techniques, nonwoven fabric manufacturers can customize the softness to meet the needs of applications such as hygiene products, wipes, and apparel.
Barrier properties refer to the ability of nonwoven fabric to prevent the passage of liquids, particles, or microorganisms, which is crucial for medical and protective applications. The barrier performance of nonwoven fabric depends on the density and porosity of the fiber web, the type of fibers used, and whether it has undergone special barrier treatments (such as waterproof or antiviral treatments). Meltblown and spunbond nonwovens are commonly used in medical and hygiene products requiring good barrier properties. Multilayer composites such as SMS (spunbond-meltblown-spunbond) typically have superior barrier properties due to the combination of functions from different layers. By carefully controlling the structure of nonwoven fabric and using specialized treatments, it can be made to possess the ability to block liquids, particles, and microorganisms, which is essential for medical protective clothing, surgical drapes, and masks.
In addition to the main performance characteristics mentioned above, nonwoven fabric also possesses many other important properties and features, such as breathability , elasticity , abrasion resistance , flame retardancy , antistatic properties , washability , sterilizability , and biodegradability.
The performance characteristics of the final product directly depend on the chosen manufacturing process and raw materials. For example, the meltblown process and the use of fine fibers give the material excellent filtration performance. Hydrophilic fibers like cotton and rayon enhance absorbency. Thermal bonding and needle punching processes can improve the strength and durability of the material.
Applications of Nonwoven Fabric in Different Industries
Nonwoven fabric, with its diverse performance characteristics, plays a crucial role in numerous industries.

In the hygiene products sector, nonwoven fabric is widely used in various components of baby diapers, including the top layer that directly contacts the skin, the absorbent layer for liquid absorption, the bottom layer that prevents liquid leakage, and the leg cuffs that provide a comfortable fit and prevent leakage. Adult incontinence products also extensively use nonwoven fabric as the absorbent core and leak-proof layer. Feminine hygiene products, such as sanitary napkins and tampons, also rely on nonwoven fabric for the absorbent layer and the body-contacting top layer. Furthermore, various wet wipes and dry wipes, whether for personal care, household cleaning, or industrial wiping, are almost entirely made of nonwoven fabric. Nursing pads and breast pads also commonly use nonwoven fabric to provide absorbency and comfort.
In the medical supplies sector, nonwoven fabric is the preferred material for manufacturing disposable medical products such as surgical gowns, masks, and protective suits due to its excellent barrier properties, breathability, and cost-effectiveness. Surgical drapes, wraps, and sterilization packaging materials also commonly use nonwoven fabric to maintain a sterile environment in operating rooms. Additionally, wound care products such as bandages, dressings, and gauze widely adopt nonwoven fabric due to its good absorbency and breathability. The filter layer of medical masks is typically made of meltblown nonwoven fabric, which can effectively block tiny particles and pathogens in the air. Additionally, medical bed sheets, pillowcases, and protective covers often use nonwoven fabric to improve hygiene levels.
In the geotextiles sector, nonwoven fabric is widely used in projects for soil stabilization, erosion control, drainage, reinforcement, and separation. For example, in road construction, railway subgrades, and dam and riverbank projects, geotextiles can effectively improve the stability and durability of the structures.
Nonwoven fabric is also an important filtration material, widely used in air filtration (such as filters for HVAC systems, automotive air filters, industrial dust removal equipment) and liquid filtration (such as filters in water treatment plants, beverage production processes, and the pharmaceutical industry). For example, the filter layer of medical masks, automotive air and oil filters, and household coffee filters and tea bags all rely on nonwoven fabric.
In the automotive industry, nonwoven fabric has a wide range of applications, including automotive interiors (such as headliners, carpets, door panels, seat covers), sound and thermal insulation materials, air and liquid filters, and tire reinforcement materials.
In the agriculture sector, nonwoven fabric is used for crop covers, plant protection, seed blankets, weed control fabrics, greenhouse shading, and root control bags to optimize crop growth, increase yields, and reduce pesticide use.
In household goods, nonwoven fabric is widely used in cleaning wipes, furniture linings, mattress padding, carpet backing, vacuum cleaner bags, and wall coverings.
Comparison of Nonwoven Fabric with Traditional Textiles
Nonwoven fabric differs significantly from traditional textiles (such as woven and knitted fabrics) in terms of cost, performance, production efficiency, and sustainability.
In terms of cost-effectiveness, the production of nonwoven fabric typically involves simpler process flows, omitting steps like spinning and weaving. This often results in faster production speeds and fewer required process steps, giving nonwoven fabric a cost advantage in many applications. However, the final cost can also be influenced by the choice of raw materials and the specific production process.
Regarding performance characteristics, nonwoven fabric may outperform traditional textiles in certain aspects. For example, in terms of absorbency, filtration, softness, and barrier properties, nonwoven fabric can achieve performance levels that are difficult for traditional textiles to match by selecting specific raw materials and manufacturing processes. However, traditional textiles typically have an advantage in terms of strength and durability, especially in applications requiring long-term use and the ability to withstand significant stress.
In terms of production efficiency, the manufacturing process for nonwoven fabric is generally simpler, allowing for higher production speeds. In contrast, traditional textiles like woven and knitted fabrics require more complex process flows, including spinning, warping, weaving, or knitting.
Regarding sustainability, the sustainability of nonwoven fabric is a complex issue that depends on the choice of raw materials and the production process. Many nonwovens are made from synthetic polymers that may not be easily biodegradable, leading to environmental concerns. However, with increasing environmental awareness, bio-based and recyclable nonwovens are becoming an important trend in the industry.
Nonwoven Fabric Market Analysis and Future Outlook
The current nonwoven fabric market shows a trend of continuous growth, especially in key application areas such as hygiene products, medical supplies, and automotive. A significant trend is the increasing demand for sustainable and environmentally friendly nonwovens, reflecting the global emphasis on environmental protection. Technological innovation is also constantly driving the improvement of nonwoven fabric product performance and the expansion of application areas. Market trends indicate a strong interplay between the demands of specific application areas (such as hygiene, medical, automotive) and broader societal concerns (such as sustainability), which is driving innovation in materials science and manufacturing processes.
Major global manufacturers in the nonwoven fabric market include Berry Global, Freudenberg Group, Kimberly-Clark, DuPont, and Ahlstrom-Munksjö. North America and Europe are the main production regions, but Asia (especially China) is also experiencing rapid growth in production and consumption. The concentration of major manufacturers in North America and Europe, coupled with the rapid growth of the Asian market, suggests a globalized market landscape with both established players and emerging regions competing for market share.
North America, Europe, and the Asia Pacific region are the main consumer regions for nonwoven fabric. Among these, hygiene products represent the largest demand sector, followed by medical, automotive, and filtration industries. Urbanization and population growth in emerging economies are expected to further drive the demand for nonwoven fabric. The dominance of hygiene products in demand highlights the importance of nonwoven fabric in daily life and public health. The growth in emerging economies indicates further market expansion in the future, creating more opportunities for manufacturers.
In the future, the development of nonwoven fabric technology and applications will likely focus on several key areas: Advances in nanofiber technology will significantly enhance the filtration performance and specialized functions of nonwoven fabric, particularly in medical and high-performance filtration applications. The development and application of bio-based and biodegradable nonwovens will become a mainstream trend to address increasing environmental demands. The research and application of intelligent nonwovens, such as in wearable technology and health monitoring, will become new growth areas. Simultaneously, the production processes for nonwoven fabric will move towards greater efficiency, automation, and sustainability to reduce costs and environmental impact. The progress of nanotechnology in enhancing performance, the dominance of bio-based materials in sustainability, and the integration of intelligent technologies in new application areas are all expected to shape the future of nonwoven fabric.
Conclusion
This report has provided a comprehensive analysis of nonwoven fabric, starting with its definition and historical development, detailing the main manufacturing processes, the characteristics of different types of nonwoven fabric, commonly used raw materials and their properties and applications, and delving into the various performance characteristics of nonwoven fabric and their influencing factors. Furthermore, the report has examined the specific applications of nonwoven fabric in different industries, including hygiene products, medical supplies, geotextiles, filtration materials, automotive, agriculture, and household goods. It has also compared and analyzed the advantages and disadvantages of nonwoven fabric relative to traditional textiles, and finally outlined the current market trends, major manufacturers and consumer regions, as well as the future direction of technology and applications.
The analysis indicates that nonwoven fabric, as an engineered textile material, plays an increasingly important role in modern society due to its unique manufacturing process and customizable performance. Its wide range of applications fully demonstrates its versatility and adaptability. With continuous technological advancements and a growing emphasis on sustainable development, nonwoven fabric will continue to innovate in the future and demonstrate its significant potential in even more fields.
Frequently Asked Questions (FAQ)
Q: What is the main difference between nonwoven fabric and traditional woven or knitted fabrics?
A: The primary difference lies in their construction. Woven fabrics are made by interlacing two sets of yarns at right angles, while knitted fabrics are created by interlocking loops of yarn. Nonwoven fabric, on the other hand, is made directly from fibers that are bonded together through various processes without weaving or knitting.
Q: Is nonwoven fabric a strong material?
A: Yes, nonwoven fabric can be engineered to have significant strength, depending on the type of fibers used, the web formation method, and the bonding process. For example, spunbond nonwoven fabric is known for its high tensile strength.
Q: Are nonwoven fabrics breathable?
A: Yes, many nonwoven fabrics are designed to be breathable. This is a property that can be controlled during manufacturing by choosing the right type of fiber, how the web is formed, and the bonding methods used. This makes them suitable for things like medical apparel and hygiene products.
Q: What are some typical applications of nonwoven fabric?
A: Nonwoven fabrics are used in a vast range of products, including diapers, medical masks, surgical gowns, geotextiles for construction, automotive interiors, filtration media, agricultural covers, and household wipes. Its versatility makes it an indispensable material in modern life.
Q: Is nonwoven fabric environmentally friendly?
A: The eco-friendliness of nonwoven fabric depends on the raw materials and manufacturing processes used. While many nonwoven fabrics are made from synthetic polymers that are not biodegradable, there is a growing trend towards using recycled and bio-based materials to improve sustainability.
Q: What are the key raw materials used in the production of nonwoven fabric?
A: Nonwoven fabrics can be made from a wide variety of raw materials, including synthetic fibers like polypropylene (PP) and polyester (PET), regenerated fibers such as rayon, and natural fibers like cotton. The choice of raw material significantly influences the final properties and applications of the nonwoven fabric.
3 Responses
It’s fascinating how nonwoven fabric skips the whole spinning and weaving process yet still manages to feel so much like traditional cloth! The fact that it’s made directly from fibers using clever bonding methods really shows how far material science has come. It’s no wonder nonwovens are used in everything from diapers to face masks they’re practical, efficient, and pretty impressive when you think about it.
“I appreciate the detailed explanation, very helpful!”
Thank you for your kind words! We’re glad the explanation was helpful to you. Feel free to reach out if you have more questions.